WPC door panel production process

A wood plastic door panel production line is an advanced manufacturing system used to produce high-quality door panels. It typically consists of several key components.
First, there is a feeding system that supplies the raw materials, which are usually a mixture of wood fibers and plastic resins. Then, a mixing and kneading unit homogenizes these materials to ensure a uniform blend.
Next, an extrusion machine forces the mixture through a die to form the basic shape of the door panel. After that, a cooling and shaping device solidifies and refines the panel's shape. Some production lines also have a surface treatment section for adding decorative finishes or textures.
Finally, a cutting and packaging system trims the panels to the desired size and prepares them for shipment. This kind of production line is highly efficient, capable of producing a large number of wood plastic door panels with consistent quality and performance.
WPC door board production line
A WPC door panel production line is a must - have for manufacturers.
It starts with raw material feeding, blends wood fibers and plastic resins, then extrudes the mixture into door panel shapes. Our production lines, as a reliable supplier, are efficient and can produce high - quality door panels. They ensure consistent output, meeting the demands of customers.
WPC door panel production line / WPC door panel making machine / WPC door extrusion machine
- WPC door making machine is applied to produce WPC door board with width of 700mm, 800mm etc, The capacity of WPC window profile extrusion production line has high capacity up to 10000kg/day, which equal to 400 -500 door boards per day.
- WPC Door Frame Making Machine Production LIne is used to produce various kind WPC profiles, such as WPC skirting board, WPC door profile, WPC corner bead, WPC folding door profile, WPC moldings and so on. the surface of WPC skirting board can be treated by printing, lamination, which can make marble, wooden design on surface of product to match with WPC floor.PVC door and window profile making machine mainly composed by conical Twin Screw Extruder, Cooling Table, Hauling Machine Cutting Machine, Stacker. With different moulds, it can produce various UPVC profile, such as: PVC window door profile, PVC wall pane PVC window sill board, cabinet door board, curtain box, PVC trucking, cable duct, PVC skirting, PVC protection corner and so on.
- The lentralized ieeding ystem is an overall solution for customers mhole plant, realizing central conveying and central controllimganocontiruous urmanned forming production. It is designed according to machine locale conditions in customer’s plant with consumption of rawmaterials,and the special requirement for auxiliary equipment. The centralized Feeding System is designed for plastic production in Injection oulding and Eztrusion industries, adopted with PlC or modularcentral automatic control methods to realize 24 hors continwous feeding and productions in each cansumption umit, With particular functions ofeach device in the system,it can perfectly meet the specific requirement for raw materials like dehumidifying, drying, conveying, dosing, mixingetc. Eqipped with multiple monitoring and protection functios, the centralized feeding system is also safe and reliable, making it the core precondition to realize unmanned factory for a modern enterprise.
Product Advantages
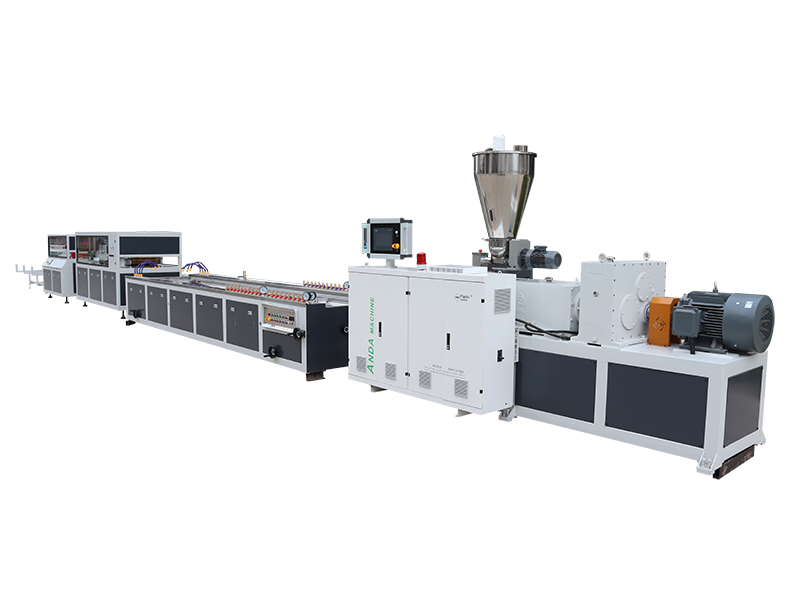
Anda Machine,provide turnkey solution for WPC door production including machine supply, installation, training ,and so on.
Firstly, these production lines are characterized by high efficiency. Advanced automated systems enable continuous production, significantly reducing the time required to manufacture each door panel. For instance, the high - speed extrusion process can quickly shape the wood - plastic composite materials into door panels, increasing output capacity.
Secondly, they ensure consistent product quality. Precise control over temperature, pressure, and raw material ratios during the production process guarantees that every door panel meets strict quality standards. This results in door panels with uniform thickness, smooth surfaces, and excellent dimensional stability.
Moreover, wood plastic door panel production lines are cost - effective. They can utilize a variety of recycled wood fibers and plastic materials, cutting down on raw material costs. Additionally, the energy - efficient operation of the equipment helps save on utility bills in the long run.
Finally, the customization flexibility is remarkable. Manufacturers can easily adjust the production parameters to create door panels in different sizes, colors, and textures, catering to diverse customer demands in the market. Overall, these production lines are a powerful tool for businesses aiming to thrive in the competitive door panel market.
Technical Specifications
A WPC door panel production line mainly applies extrusion, compounding and molding technologies. Extrusion pushes the blended wood - fiber and plastic - resin mixture through a die to form the panel shape. Compounding evenly mixes the raw materials for consistent quality. Molding refines the shape and texture, ensuring the final product meets industry standards.
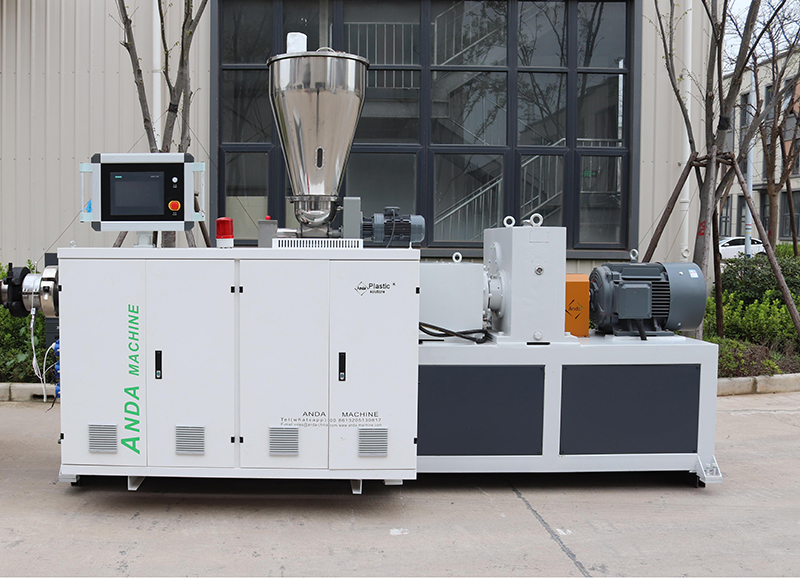
Videos of WPC door and frame production line
Application
WPC door panel production lines have wide applications. They are commonly used in residential construction for interior and exterior doors, providing durability and aesthetic appeal. In commercial buildings like offices and hotels, the produced panels are used for partitioning and decorative doors. Additionally, they find use in furniture manufacturing, such as wardrobe doors, due to their resistance to moisture and easy maintenance.
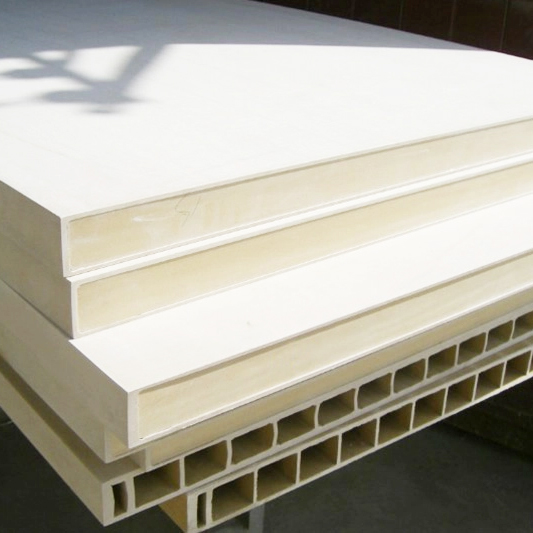
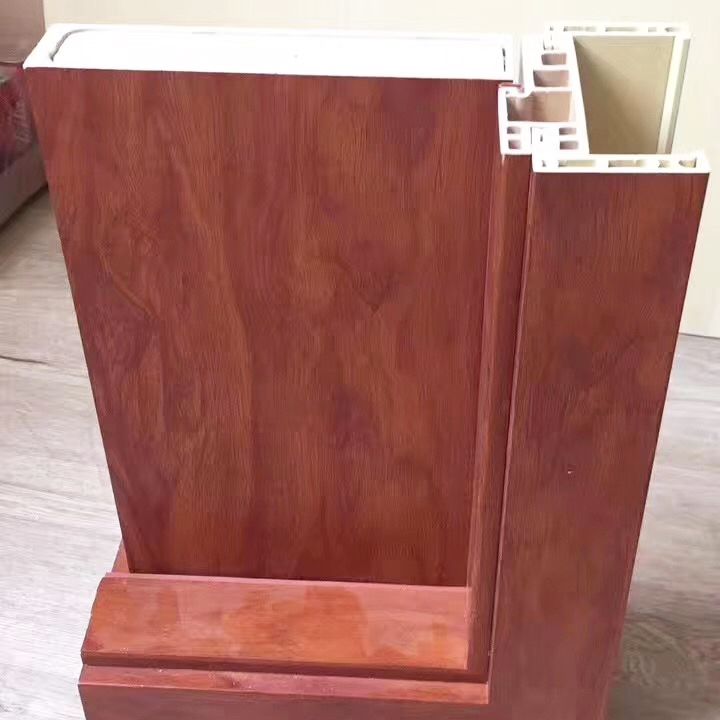
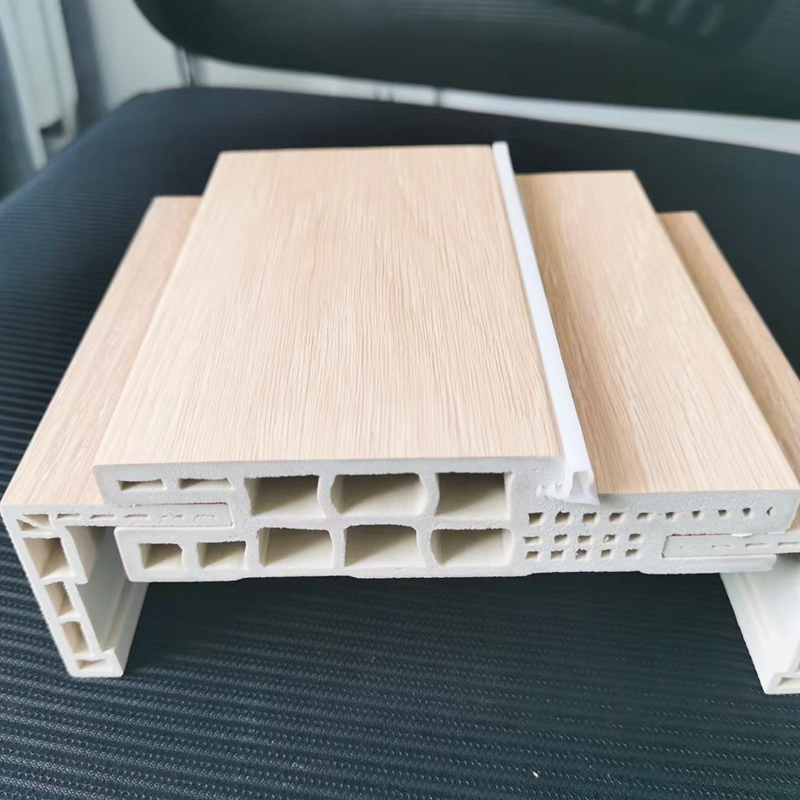
FAQs
What are the raw materials for the production line?
Usually, a mixture of wood fibers, such as sawdust or wood shavings, and plastic resins like polyethylene or polypropylene is used.
How to ensure the quality of door panels?
By precisely controlling the ratio of raw materials, temperature, and pressure during the production process, and conducting regular quality inspections.
Can the production line be customized?
Yes, it can be customized according to different production requirements, such as the size, shape, and color of the door panels.
What is the production capacity of the production line?
It varies depending on the model and configuration of the production line, generally ranging from several hundred to several thousand square meters per day.
How to maintain the production line?
Regular cleaning, lubrication of moving parts, and timely replacement of worn - out components are required.
Is the production line energy - efficient?
Modern production lines are designed to be energy - efficient, using advanced heating and cooling systems to reduce energy consumption.
What are the advantages of wood - plastic door panels?
They are waterproof, fire - resistant, termite - proof, and have good dimensional stability and low maintenance costs.
Can the production line handle recycled materials?
Many production lines can use recycled wood fibers and plastic materials, which helps to reduce costs and environmental impact.
Related Blogs
- How PVC Edge Banding Tape Making Machines Enhance Production Efficiency
Introduction When it comes to furniture and cabinetry, the finishing touches can make all the difference. One such finishing touch is the use of PVC edge banding tape. This versatile material not only enhances the aesthetic appeal of your furniture but also protects the edges from damage. But the qu
2025-02-18
- What is the thickness of PVC wall cladding?
Introduction When it comes to home improvement and construction, one of the most frequently asked questions is: "What is the thickness of PVC wall cladding?" Understanding the dimensions and properties of PVC wall cladding is crucial for both aesthetic and functional purposes. In this article, we wi
2024-07-05
- Enhancing Curb Appeal with Durable and Customizable PVC Soffit Panels
Introduction When it comes to enhancing the curb appeal of your home, one often overlooked element is the soffit. The soffit, located under the eaves of your roof, plays a crucial role in both aesthetics and functionality. One of the best materials for this purpose is PVC, thanks to its durability a
2024-07-05
- Choose the Best PVC Marble Slab Making Machine
Introduction In the world of construction and interior design, the demand for high-quality, aesthetically pleasing materials is ever-growing. One such material that has gained significant popularity is the PVC marble slab. These slabs are not only durable but also offer a luxurious appearance at a f
2024-07-05
Keep in touch with us
Mob:+86-18083723406
E-mail:info@anda-china.com